A Split Phase Induction Motor is a single phase motor consists of a stator and a single-cage rotor. The stator has two windings i.e. main winding and an auxiliary winding. The auxiliary winding is also known as starting winding. In construction, these two windings are placed 90° apart in space. The Split Phase Induction Motor is shown in figure 1. This motor is also known as Resistance-start motor.
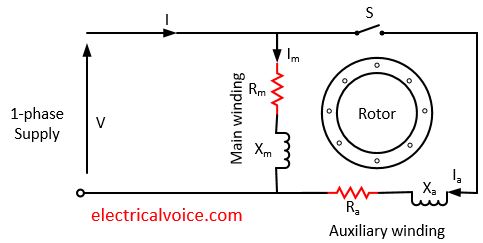
Rm = main winding resistance
Xm= main winding inductive reactance
Ra = series resistor connected in the auxiliary winding
Xa = auxiliary winding inductive reactance
S = centrifugal switch or relay
The main winding in this motor has low resistance and high inductive reactance. The auxiliary winding has high resistance and low inductive reactance.
Working of Split Phase Induction Motor
When the stator windings are energised from a 1-phase supply, the main winding carries current Im and the starting winding carries current Ia. As main winding has low resistance and high inductive reactance, Im lags behind the supply voltage V. Also, auxiliary winding has high resistance and low inductive reactance, current Ia is closely in phase with the supply voltage. Therefore, there is a time-phase difference between two currents. These two currents are out of phase (25° to 30°) and produce a weak rotating magnetic field which starts the motor. Since currents in two windings are not equal, the rotating magnetic field is not uniform. Hence, the starting torque is small.
The main and auxiliary windings are connected in parallel during motor starting. When the motor reaches speed about 70 to 80 % of synchronous speed, the auxiliary winding disconnects from the supply by centrifugally operated switch S.
The phasor diagram for this motor is shown in figure 2.

The torque-speed characteristic of this motor is shown in figure 3.
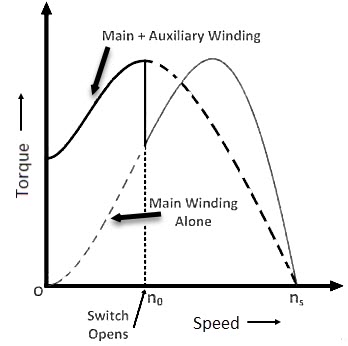
Note:
1. The reversal of the direction of rotation of this motor is possible by reversing the line connections of either main winding or the auxiliary winding. This can be done when the motor is at standstill condition.
2. These motors are essentially constant-speed motors. The speed variation is 2 to 5 % from no-load to full-load.
3. Such a motor can be operated with a power factor ranges between 0.55 – 0.65.
4. The percent slip for such motors is about 4 to 6 %.
5. The starting torque is 1.5 to 2 times the full load torque and the starting current is 6 to 8 times the full-load current.
6. The power ratings of such motors are from 60 Watts to 250 Watts.
7. They have an efficiency of 50 – 70 % and overload of 50%.
Applications
The Split-Phase Induction Motor is suitable for easily started loads.
1. It is used to drive fans, blowers, centrifugal pumps, domestic refrigerators, washing machines, oil burners, small machine tools, food mixers, lathes, etc.
2. As they have moderate starting torque and low starting current, so they are seldom used for drives requiring more than 1 kW.