![]() |
Figure. RVDT |
Working Principle of RVDT
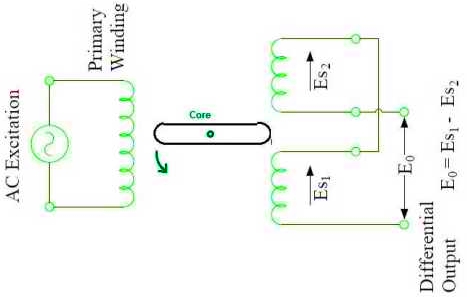
The reluctance seen by the primary mmf changes with the rotation of core by shaft. This results in change in the magnetic flux with rotation of the shaft. Due to this change in magnetic flux with rotation of core, the flux linkage of secondary winding also changes. Therefore, as per the transformer action, an emf is induced in secondary winding. The magnitude of induced emf will depend on the rate of change of rotation. The more the rate of change of rotation, the more will be the rate of change of flux and hence more emf will be induced.
As can be seen from the figure 1, the two secondary winding are connected in series but in phase opposition. This is done to get a single output voltage from the transducer. If Es1, Es2 and E0 be the emf induced in the two secondary winding S1 & S2 and output voltage respectively then
E0 = Es1 – Es2
Under normal condition of RVDT, the flux linkage of both the secondary winding are same due to their symmetrical placing w.r.t. primary and core. Therefore, the induced emf Es1 and Es2 are equal and hence output voltage E0 of the transducer in such condition is zero. Therefore, normal position of RVDT is called NULL position.
Clockwise rotation of core causes an increasing voltage Es2 in one of the one secondary winding while counter clockwise rotation leads to increase in voltage Es1 of another secondary winding. Thus the direction as well as magnitude of angular rotation can be ascertained from the magnitude and phase of transducer output voltage. Phase of transducer output voltage means whether (Es1 – Es2) is positive or negative.
In case of anti-clockwise rotation of core, the value of Es1 will be more than that of Es2 and hence (Es1 – Es2) will be positive. In this case we say that output voltage E0 is in phase with the primary voltage. With the same logic, when core is rotated in clockwise direction, the output voltage will be negative i.e. out of phase with primary voltage.
Summary: The secondary windings are connected in series opposition. At the null position, output voltages of secondary windings S1 and S2 are equal. Hence the net output of RVDT is zero. When there is a clockwise rotation, it produces an increasing voltage of a secondary winding of one phase. When there is an anti-clockwise rotation, it produces an increasing voltage of a secondary winding of opposite phase.
Applications of RVDT
Excercise
Q. Describe the working of RVDT with the help of neat circuit diagram.