As PCB mass production and global electronics manufacturing are on the rise, choosing the right solder for PCB assembly is still a key selection process. The selection between leaded solder and lead free solder directly has pitfalls in the manufacturing process, environmental compliance, product quality as well as long-term reliability. In this article we will take a look at lead free and leaded solder, how they are different, the pros and cons of each, and what you need to consider when determining which to use in your PCB assembly (PCBA) projects. Here are insights into the difference between lead free PCBA and leaded PCBA.
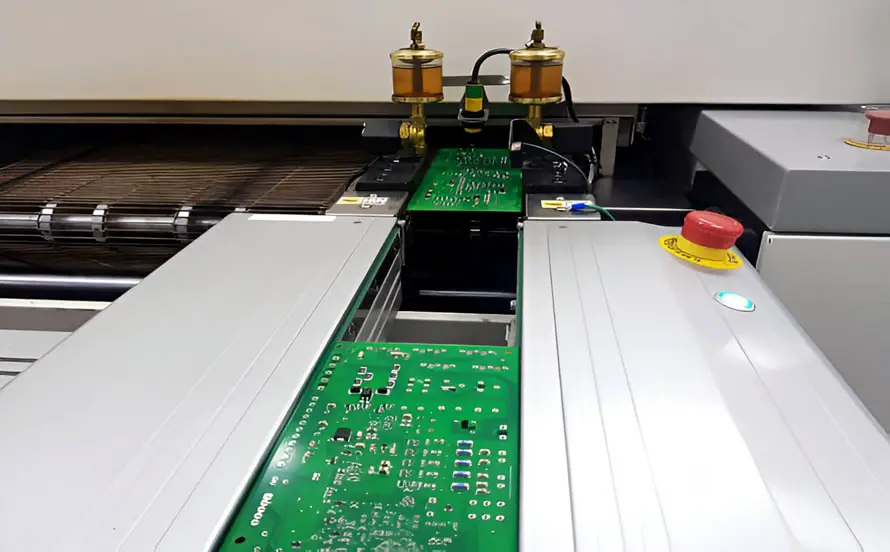
What is Lead Free and Leaded Solder in PCBA?
Leaded solder contains tin and lead, and its characteristics are low melting point and excellent connection reliability. However, it is toxic and does not comply with international RoHS regulations.
Lead free solder uses metals such as silver and copper instead of lead, which is environmentally friendly, but it requires a higher melting temperature and the welded nodes are relatively fragile.
Lead free PCBA and Leaded PCBA have different applications due to their properties.
Lead-Free vs. Leaded Solder: What’s the Difference?
Lead free Solder: If a solder is lead-free, it means the solder doesn’t have lead in it. Having tin, copper, silver or other metals is what makes it. Usually Sn99.3 (tin and copper) or Sn 96.5 (tin, silver, and copper, 3.0 silver; 0.5 copper). Concerning lead free PCBA, soldering melting points are typically higher (217–220°C) than those of leaded solder, and the lead free assembly process needs to be adjusted.
Leaded Solder: Leaded solder is the industry standard for PCB assembly. Typically a Sn60 / Pb40 mixture of tin and lead for its ease of use, good wettability, and low melting point of approximately 183°C, lead solder is mixed with a number of other elements to enhance its solderability and other performance trait characteristics. Containing lead, leaded solder is a strong, reliable joint, and has been chosen for high-reliability applications including aerospace and military electronics.
Properties of Lead Free and Leaded Solder
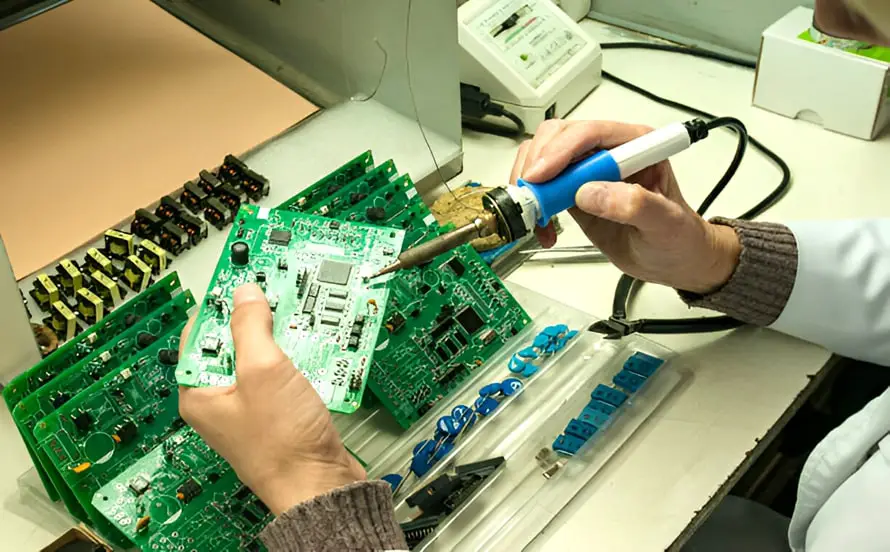
1. Melting Point and Thermal Properties
The major difference between leaded and lead free solder is their melting point. Leaded solder melts at about 183°C and lead free solder melts at a higher temperature, about 217°C to 220°C. The higher melting point of solder used in the lead free PCB assembly induces control problems and may necessitate changes in equipment and material. This difference impacts various aspects of the assembly process.
- Reflow Profiles: The solder used in the lead free PCB assembly has a higher reflow temperature, therefore the heating profile has to be shifted and the temperature has to be controlled more exactly to prevent components from burning out during the lead free PCBA.
- Heat Tolerance of Components and Substrates: The higher temperatures of lead free solder require that the components and the PCB materials be able to withstand it. It can result in component warping, delamination, and component damage during the lead free PCB assembly.
- Energy Consumption: This means that reflow ovens and wave soldering machines should climb the necessary temperature for lead free soldering. Therefore, lead free PCBA becomes more expensive in terms of energy consumption and equipment wear.
2. Mechanical Strength
- Leaded Solder: The ductility and flexibility of the solder used in the lead free PCB assembly allow it to accommodate thermal strain and mechanical strain. Where the material experiences temperature fluctuations, leaded joints are more durable compared to the solder used in the lead free PCBA.
- Lead Free Solder: The resistance of lead free joints is more likely to decrease with mechanical stress or thermal cycling, which often exists in the lead free PCB assembly. Over time, however, the brittleness gets progressively worse, especially in applications that face thermal expansion and shock. As solder used in the lead free PCBA has improved in quality, newer alloys yield better mechanical attributes, and an application’s qualified selection of leaded or lead free solder depends on the application’s mechanical requirements.
3. Wet and Fill Characteristic
The creation of a solder joint greatly relies on both the wetting and flow behaviour. The solder used in the lead free PCB assembly offers different properties from leaded solder.
- Leaded Solder: Wetting and flow characteristics are excellent for smooth, even joints. Lead solder ideally melts at a lower temperature compared to the solder used in the lead free PCB assembly. In silver eutectic lead, solder flows across component pads to achieve good coverage and joint strength.
- Lead Free Solder: Concerning lead free PCBA, colder wetting properties of lead free solder are poorer, and may need more flux to achieve the same coverage. You can increase voids and potentially weaken joints if not controlled properly. Due to its non-toxic behavior, the solder existing in the lead free PCB assembly is preferred in most consumer electronics.
Basic Considerations about Choosing Lead Free and Leaded Solder in PCB Assembly
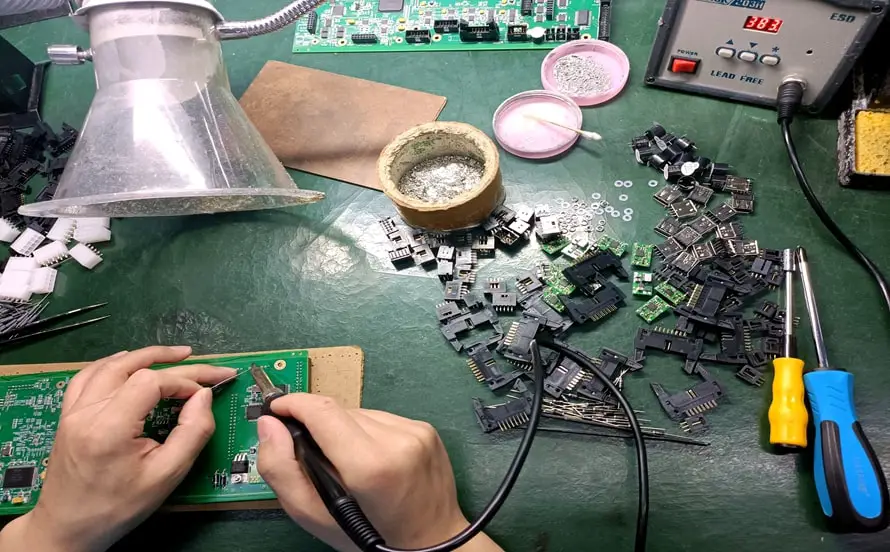
1. Lead Free and Leaded Solder Cost
The major driving factor behind the higher prices of solder used in the lead free PCBA is the cost of alternative metals used, in particular silver and copper. In addition to material costs, lead free PCB assembly can incur added expenses in equipment upgrades, energy consumption, and process adjustments. While these costs are high, lead free PCBA has gotten cheaper as manufacturers and equipment processes have evolved.
- Material Costs: Usual solder alloys used in the lead free PCBA are more expensive because of the use of alternative metals(Silver and copper).
- Equipment Wear: Relatively high processing temperatures of lead free PCB assembly can result in more frequent maintenance and shorter oven lifespans (reflow ovens)
- Yield and Rework Costs: The use of lead free PCBA can result in higher defects and more rework costs. Ideally mitigated through process control and advanced reflow ovens will increase the initial setup cost.
2. Health and Safety
- Lead free Solder: By removing the risks of lead exposure, lead free solder is mostly used. It is crucial to see that alternative metals in the lead free PCB assembly, such as silver and copper, are handled properly to minimize metal particulate exposure risks.
- Leaded Solder: The lead solder is dealt with with strict safety protocol. By doing this, one will ensure that there is safety and adequate ventilation, among others to reduce exposure risks. Lead poisoning is still a concern among the workers repeatedly who are subjected to soldering fumes compared to the workers in the lead free PCBA production line.
3. Environmental and Regulatory Factors
Environmental regulation is one of the main driving forces for lead free solder adoption. Guided by the RoHS directive from 2006, the use of particular hazardous components such as lead, is prohibited in electrical or electronic equipment. Lead exposure is not just a domestic issue but it’s an international problem, and many countries have taken the same approach for minimizing its environmental impact and limiting health risks, by restricting lead from entering the electronic landscape.
4. Choosing a Solder for the Project
The use of leaded and lead free solder must be decided on factors of reliability requirements, cost, regulatory compliance and environmental considerations. Here’s a summary of when to consider each type.
- Choose Lead Free Solder if: You need to comply with environmental regulations, like RoHS. If It is a consumer electronics or general-purpose product, the requirement for thermal cycling and high reliability is less.
- Choose Leaded Solder if: The devices target high-reliability applications such as aerospace, military, or medical. Ease of soldering and reduced thermal stress is a priority. Owing to production volume, the material lead could be handled and disposed of with safety standards.
Applications of Lead Free and Leaded Solder
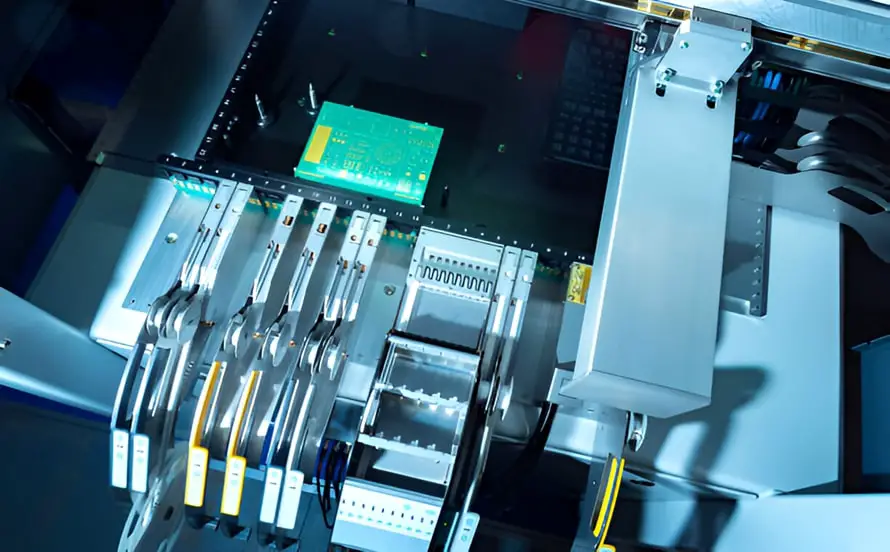
The decision between leaded and lead free solder depends a lot on long-term reliability, especially in the case of applications with high reliability requirements.
- Consumer Electronics: And by regulations and product life cycles, lead solder materials are adequate for consumer electronics compared to the solder used in the lead free PCBA. For those applications, the minor reliability comes cheap and with large benefits on environmental grounds.
- Automotive and Industrial: The reliability standards for automotive and industrial electronics that lead free jointing must meet are strict, and the jointing should have an appropriate solder structure, especially for harsh environments. Recent developments in lead free alloys (e.g. silver and bismuth) have made solder used in the lead free PCB assembly applicable for some of such uses.
- Aerospace and Defence: Lead solder is used instead of standardized solder for applications where high reliability is demanded, for instance in the aerospace, defence, and medical device segments. In many of these cases, applications require long periods of working from reliable components in harsh environments, so leading solder is a better option for its durability and its thermal cycling resistance.
Conclusion
In selecting between lead free and leaded solder, there are many implications to choose leading from regulatory compliance to performance and cost. Leaded solder is still essential in high-reliability applications while solder used in the lead free PCBA is the common standard in consumer electronics because of the environmental concerns. There are unique properties for each different type of solder, and selecting the right one according to our application is very necessary.